The qobeo solution
qobeo is a 3D CFD software aimed at the simulation of industrial processes (heating and cooling)
qobeo is a help decision making tool for heating/cooling process optimization. As a full 3D CFD software, qobeo is 100% dedicated to heating and cooling, surface treatment processes simulation, whatever the geometry, whatever the equipment.
Heating or cooling rate of workpieces are then easily analyzed.
qobeo is developped by Sciences Computers Consultants, in partnership with the CEMEF, (from Mines ParisTech).
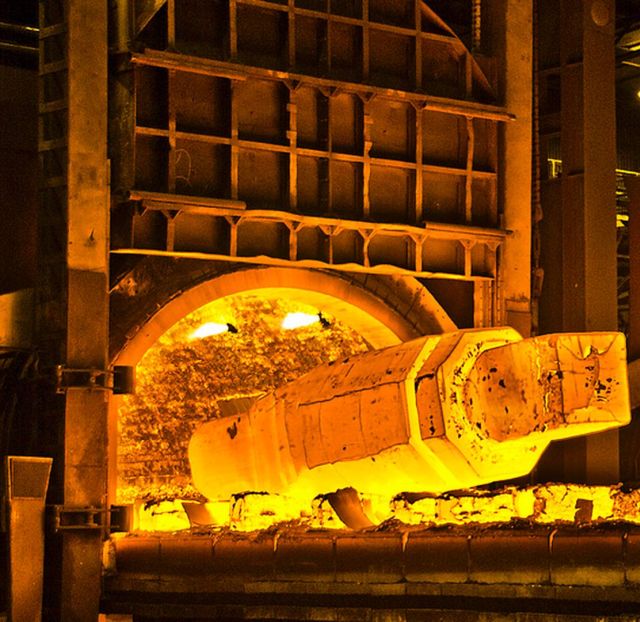
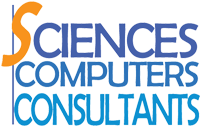
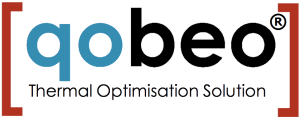
A few things we’re great at
The indeep process analysis provided by qobeo offers new keys for deeply understanding and analyzing the process complexity.
Simulation offers a new highlight on industrial processes. Getting quantifiable results and values about flow, temperature, velocity, heating/cooling speed, power and energy provide a new focus for optimizing industrial processes. qobeo, as a real toolbox gives you now this new vision.
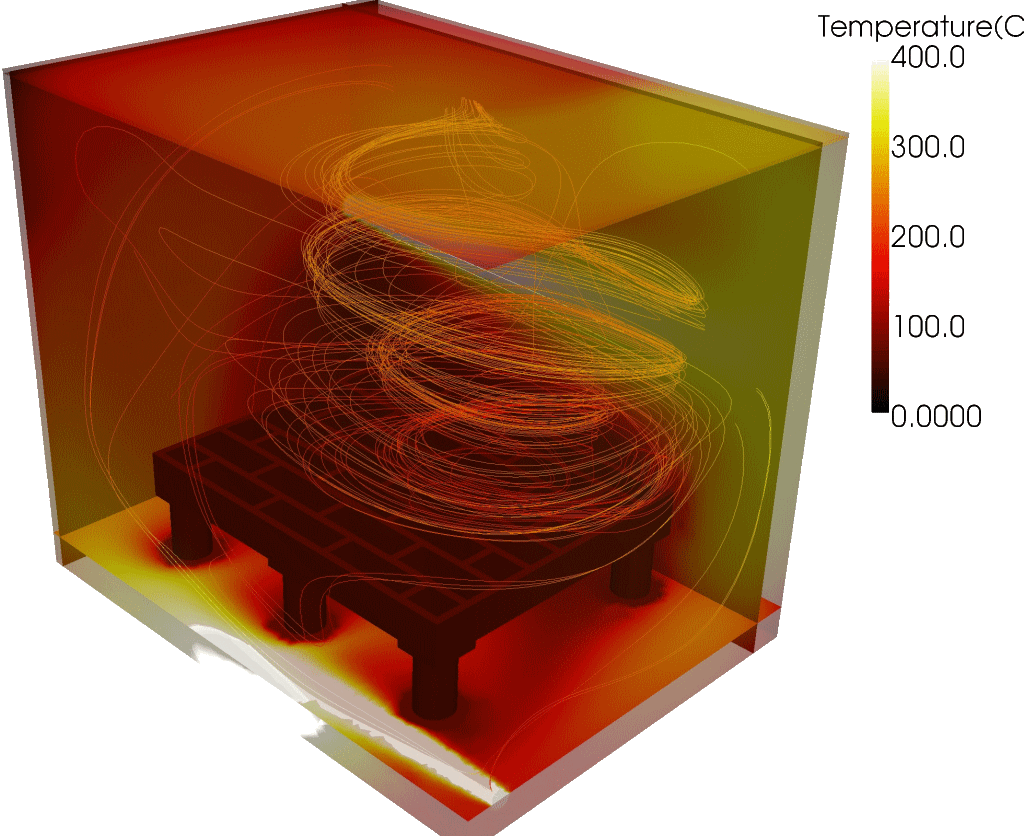
Advanced CFD Software
The qobeo software uses different solvers for computing the CFD flows into furnaces/quench tanks. Thanks to coupling of hydro, CFD and thermal models, qobeo is now able to compute the evolution of the fluid and its impact on the workpiece.
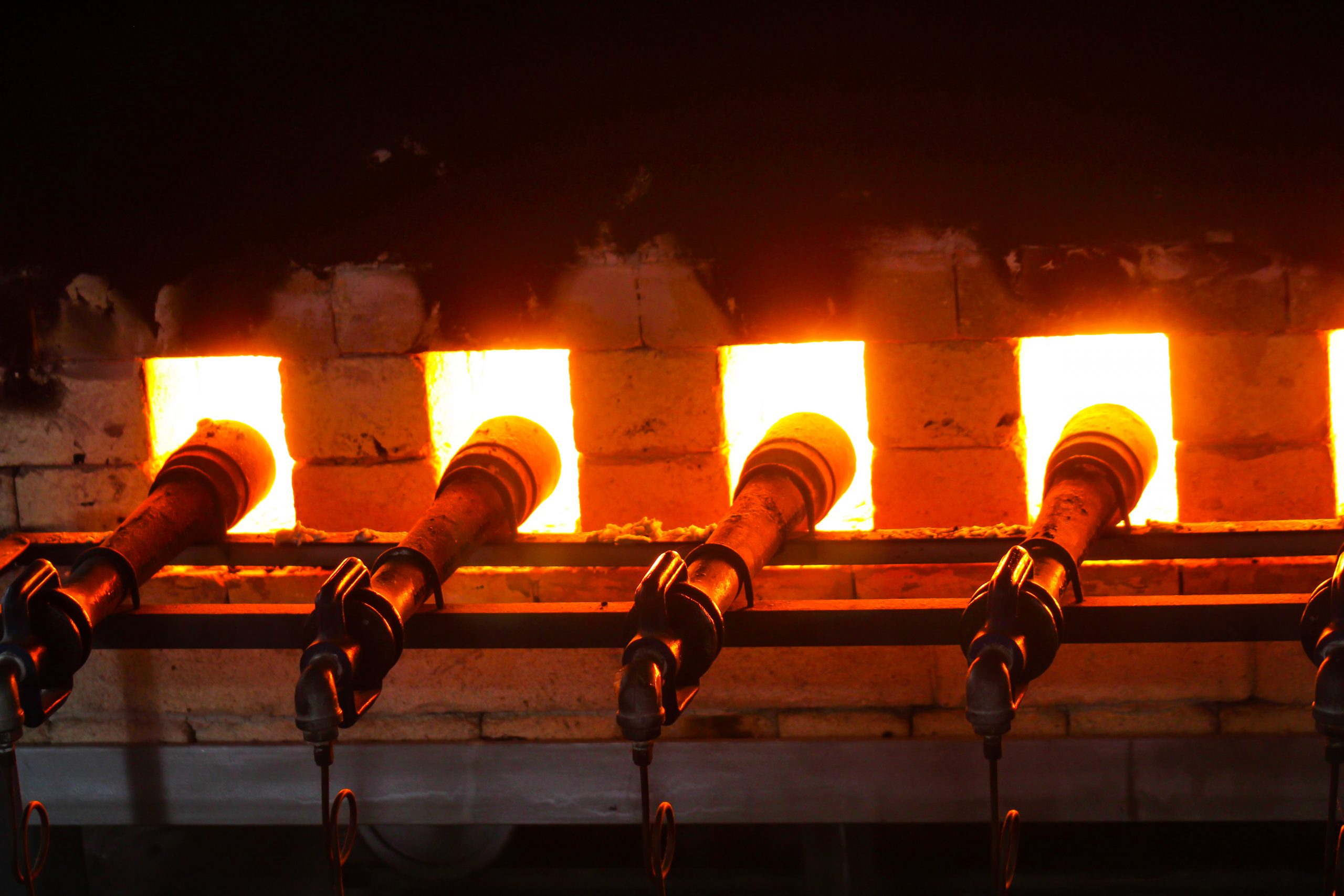
Complex physics
Different version of qobeo are now available to analyse specific phenomena. Radiation, heating and cooling, cooling and quenching are tackled with our qobeo packages.
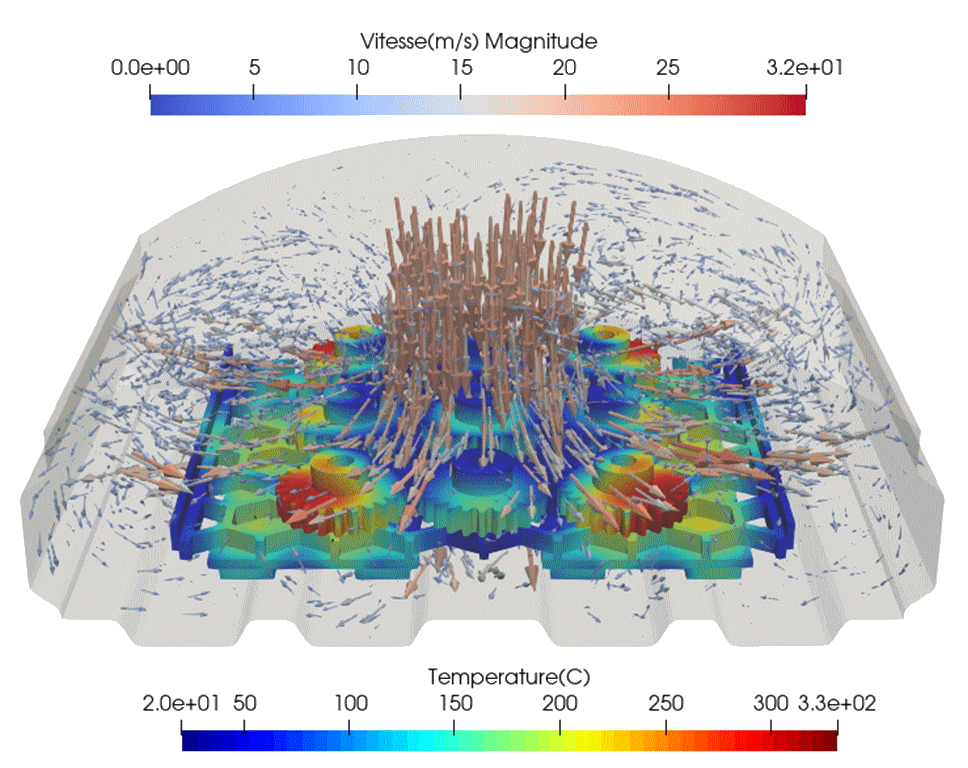
All in one environment
qobeo handles now all your need for the numerical modeling or your equipments. The integrated and automatic remesher uses the 3D description (provided as CAD file) to generate the mesh of the computing domain and the different resources (burners, hood, doors, sensors… ).
Get started
Install, deploy, compute
qobeo proposes 3 packages : S2S, AIR, BUB. Each version tackles very specific phenomena. Packages are designed for offering the right level of physical/numerical models according to the observed applications, with :
- S2S : for radiation under vacuum
- AIR : for heating and cooling (natural/forced convection), PID regulation, thermal computation for solids and gas
- BUB : for cooling and quenching, with liquid quenching, vaporization, Hydrodynamic computation & thermal coupling
Easier, faster than ever
qobeo is 100% parallel, providing faster computations
Remeshing stages, hydro, CFD and thermal computation are 100% parallel, thanks to the use of the CimLib library (provided by the CEMEF), making qobeo faster, more accurate and also easy to handle.
All the qobeo applications are hosted by the SCC-Lab platform, used as a real toolbox for offering all the modules you need to import your CAD files, realize the meshing, prepare the simulations and run the simulations.
Services
Software license
SC-Consultants sales the qobeo software license. According to your need, process and applications, appropriated packages are available. Onpremise license or cloud based model (soon available) can be purchased.
Consulting
Consulting services are performed by SC-Consultants. Needs, specifications and targets are discussed during a first round. Adjustments and iterations are made until getting a formal service proposal to analyze your process and give you the main keys of its optimization.
Training and support
Standard training and technical support are included into our license package. Specific contents can be defined upon requirements. Feel free to contact our team for more details.
What are you waiting for?
It’s always worth using numerical simulation than applying the classic trial/error method. Just contact our team for a full presentation or demo of the qobeo software
Some applications
qobeo can handle any kind of geometries for various applications. In the few hereafter examples, qobeo is used for computing the CFD flows inside specific and various equipments AND also the heat exchange. Are thus proposed as results : cooling/heating velocity, temperature, velocity fields and so on.
Find here our last conference and papers:
- Optimizing gas flow in a furnace through numerical simulation: a case study using qobeo, S. EL AOUAD; G. LISSONI; L. RATTE; J-C. BIHR; L. SARDO – ECHT 2025 Conference in Prague
- A heat treatment process optimization : coupling qobeo and FORGE, S. EL AOUAD; G. LISSONI; L. RATTE; L. SARDO ; J. BARLIER; P. LASNE – Mattris A3TS Congress 2025 in Dijon
- A sustainable approach to decarbonization in industrial heat treatment process, S. EL AOUAD; G. LISSONI; L. RATTE ; L. SARDO – A3TS Congress 2024 in Toulouse
Our References and partners
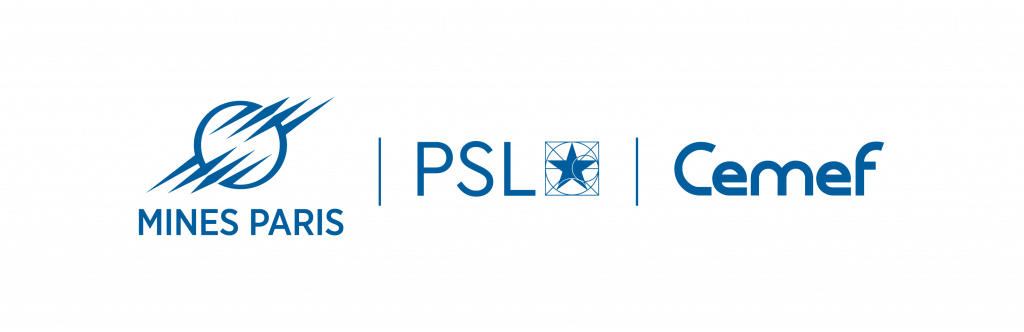
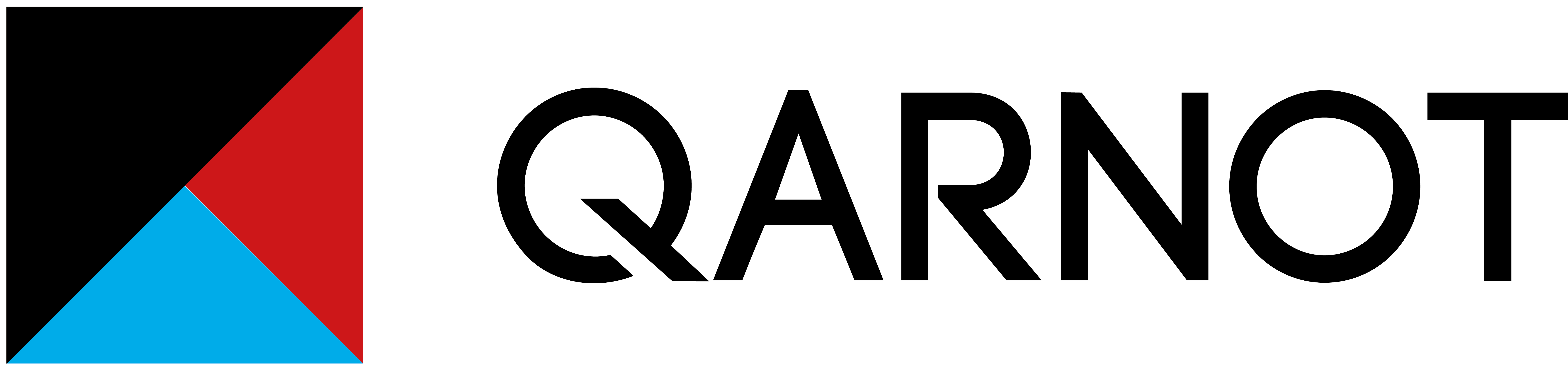
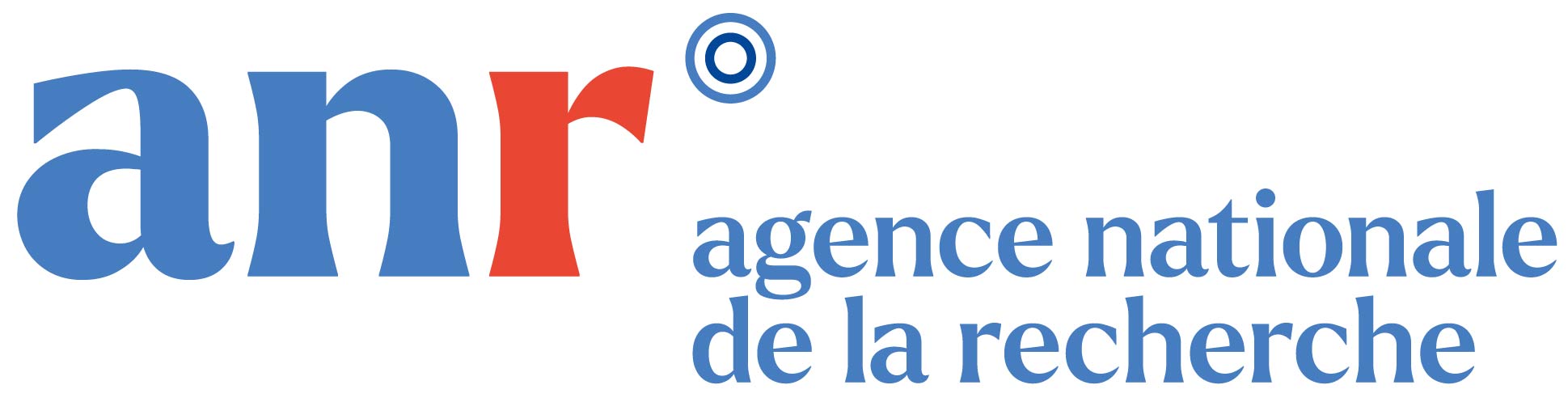
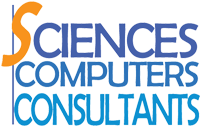
Contact us
For any questions, projects or ideas, feel free to contact our team : we all remain at your disposal